中国煤制天然气产业除了面对环保、资源、资本等问题之外,技术、装备国产化是产业发展、项目示范的重中之重。关键技术国产化替代、项目投资大幅下降的好戏已经在煤制油、煤制烯烃等领域屡屡上演。而这次即将为煤制天然气产业带来“颠覆式“革新的是一项新型甲烷化技术——无循环甲烷化工艺技术(NRMT,Non-recycle Methanation Technology)。在近日中国石油和化工工业联合会组织,由金涌院士任专家组长的科技成果鉴定会中,鉴定委员会一致认为由北京华福、大连瑞克、中煤龙化联合开发的无循环甲烷化新技术“综合水平达到国际先进水平”,实现甲烷化技术国产化,打破国外技术的垄断。
颠覆在哪里
目前工业化的甲烷化技术主要有英国Davy甲烷化技术、丹麦Topsoe甲烷化技术和德国Lurgi甲烷化技术。截至目前,我国已开车和在建的4套煤制天然气项目全部引进国外甲烷化技术。煤制天然气甲烷化技术的国产化迫在眉睫。
现有甲烷化技术都设有循环气压缩机,通过循环气的稀释来调节反应温度,均为循环甲烷化工艺,也就带来能耗高。与该类技术相比,“无循环甲烷化工艺技术“具有如下优点:
(1) 投资降低,取消了循环气压缩机系统,节省投资20%以上;
(2) 系统节能,与循环工艺相比,运行能耗降低25%以上;以13亿方煤制天然气装置为例,仅节能就节省成本达2000万—3000万元/年;
(3) 通过氢碳比分级调节,系统飞温的可能性降低,运行更加平稳、安全,产品质量更趋稳定。
无循环甲烷化工艺(NRMT,Non-recycle Methanation Technology)由北京华福、大连瑞克、中煤龙化合作开发。在以上方面取得的重大突破意味着甲烷化技术国产化时代已经来临!现有甲烷化技术国外垄断的局面真正被打破。这是国产化甲烷化技术的一次完美“逆袭”,也将助力中国煤制天然气竞争力进一步提升,大幅提振中国煤制天然气产业信心!
奇迹的发生看似偶然,其实其中往往蕴含必然。
北京华福工程有限公司在煤化工、石油化工、炼油领域深耕多年,在能源化工领域业绩卓著——华福EPC+M总承包的乌兰大化肥项目,产能达135万吨/年合成氨、240万吨/年尿素;华福参与联合项目管理(IPMT)的神华宁煤400万吨/年煤炭间接液化项目是国内最大的煤化工项目;同时华福工程拥有数十个煤制甲醇、煤制合成氨、尿素以及煤炭清洁利用项目。
另外,华福承接的翔鹭石化450万吨/年PTA项目,为世界规模最大的PTA生产线,已列入国家石化产业调整振兴规划;华福设计的山东京博25万吨/年混合烷烃脱氢项目,以液化气为原料,生产环氧基丙烯和化工级MTBE,为国内第一套、世界第二套C3/C4混合烷烃脱氢项目;华福采用“浮式LNG液化再气化储存装置管线柔性设计技术”设计的美国BV公司船用LNG装置为世界首套浮式LNG装置。
技术研发历程回顾
无循环甲烷化工艺技术的完美“孕育”,背后是北京华福研发团队还长达数年智慧和心血的潜心投入。以下是无循环甲烷化工艺技术研发历程首次公开全“剧透”。
一、研发里程碑节点
2008年9月,项目研发启动;
2009年10月,催化剂研制成功;
2011年10月,实验室小试完成;
2013年4月,中试设计启动;
2014年2月,中试装置建成;
2014年10月,中试装置单级反应器投料;
2014年11月,中试装置全流程打通;
2015年10月,中试装置连续稳定运行并标定;
二、投料试车
中试装置建设于中煤龙化公司厂区内,依托厂区原料气、中压蒸汽、中压氮气、低压氮气、锅炉水、循环水以及电力等公用设施。
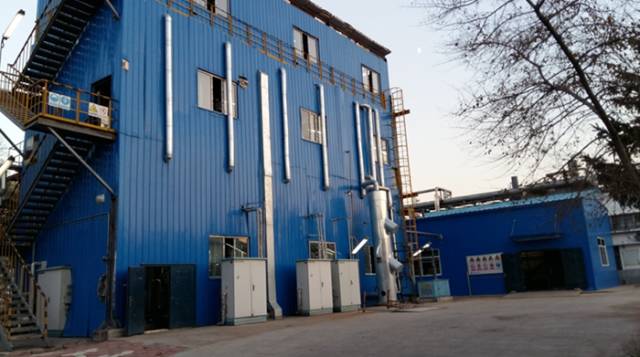
原料气有两种,一种为甲醇系统的膜分离富H2气,另一种为低温甲醇洗后的净化煤气即富CO气。
装置规模:原料气处理量1000Nm3/h,产品合成天然气产量333 Nm3/h。
产品规格:CH4>95%,H2<2%,CO<0.01%,CO2<1%。
1、全流程打通(第一阶段工作)
2014年11月14日-12月5日(在-30℃的情况下)进行了系统第一次投料试运行,各方面运行数据正常、平稳,全流程打通,连续运行20天。
2、装置测试(第二阶段工作)
2015年6月13日至2015年6月16日进行了为期3天的装置测试, 产出了合格产品。
3、连续稳定运行(第三阶段工作)
2015年10月17日1:40装置第二次投料,8:30产品气甲烷含量达到了95.89%,中午11:30左右开启了产品气回收系统,至此产品气正式并入了产品天然气管网。
10月17日至10月23日(现场标定前)部分运行数据:
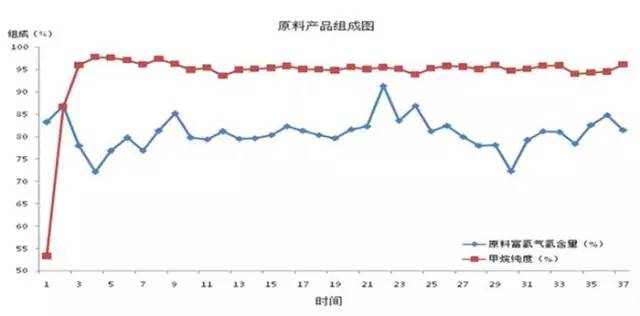
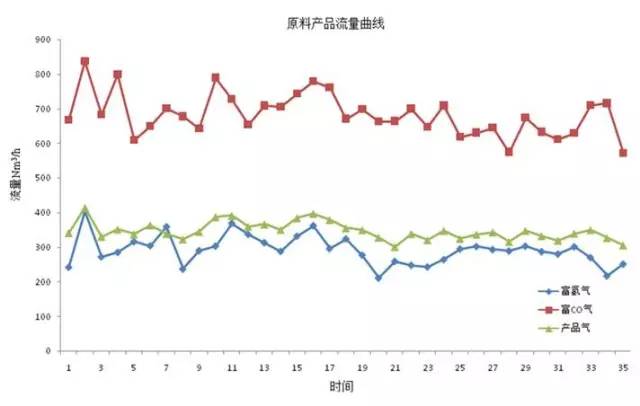
由图可以看出,自装置投料后,短时间内实现了稳定运行,产品质量达标,装置运行期间整体稳定,原料气供气量约为1000Nm³/h。产品CH4含量在95%以上,最高达到了97.79%,CO未检出,CO2含量